FFS heavy packaging film: three-layer vs. five-layer, a scientific selection guide that buyers must read
As a decision maker in the global procurement field, are you struggling with the specifications of FFS heavy packaging film? What is the difference between three-layer and five-layer? How to achieve the best packaging effect at the lowest cost? This article will analyze it for you from a scientific perspective to help you make decisions easily.
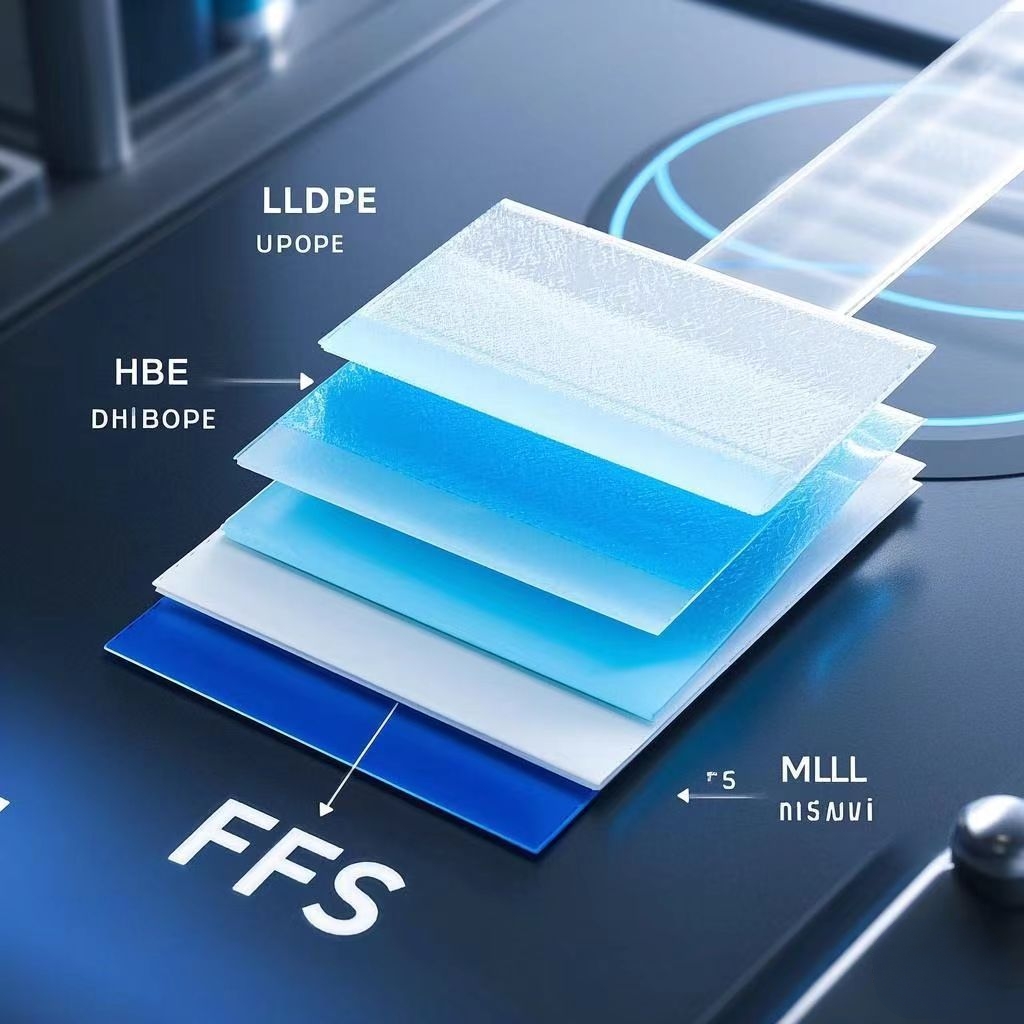
1. The structural secret of FFS film: the number of layers does not double the performance
The core functions of FFS heavy packaging film (Form-Fill-Seal) are protection + sealing + ease of use, and its performance depends on two key factors:
1 Material formulation (such as the ratio of LLDPE and HDPE)
2 Interlayer collaborative design (functional division of each layer)
The three-layer film structure (classic design) includes:
Outer layer: wear-resistant LLDPE (linear low-density polyethylene), wear-resistant and UV-resistant
Middle layer: high-strength HDPE (high-density polyethylene), enhanced mechanical strength
Inner layer: heat-sealable mLLDPE (metallocene polyethylene), heat-sealable and anti-pollution
The five-layer film structure (functional superposition) is to add two layers on the basis of three layers, a barrier layer (moisture-proof/anti-static) and an adhesive layer (enhanced interlayer bonding)
As the High-quality packaging film supplier, my company uses the German Reifenhauser co-extrusion technology. Modern three-layer films have been able to achieve 97% of the performance of five-layer films through molecular-level optimization, with significant cost savings.
2. The golden rule for selecting the number of layers: only by matching according to demand can you save money
Scenario 1: Conventional industrial product packaging (accounting for 80% of demand)。
Applicable products: chemical raw materials (fertilizers, resins, chemical granules, etc.), food-grade raw materials (starch, sugar, rice, corn, etc.), feed, building materials and auxiliary materials (cement additives, gypsum powder), granular materials, powder materials, etc., packaging specifications of 25kg and below
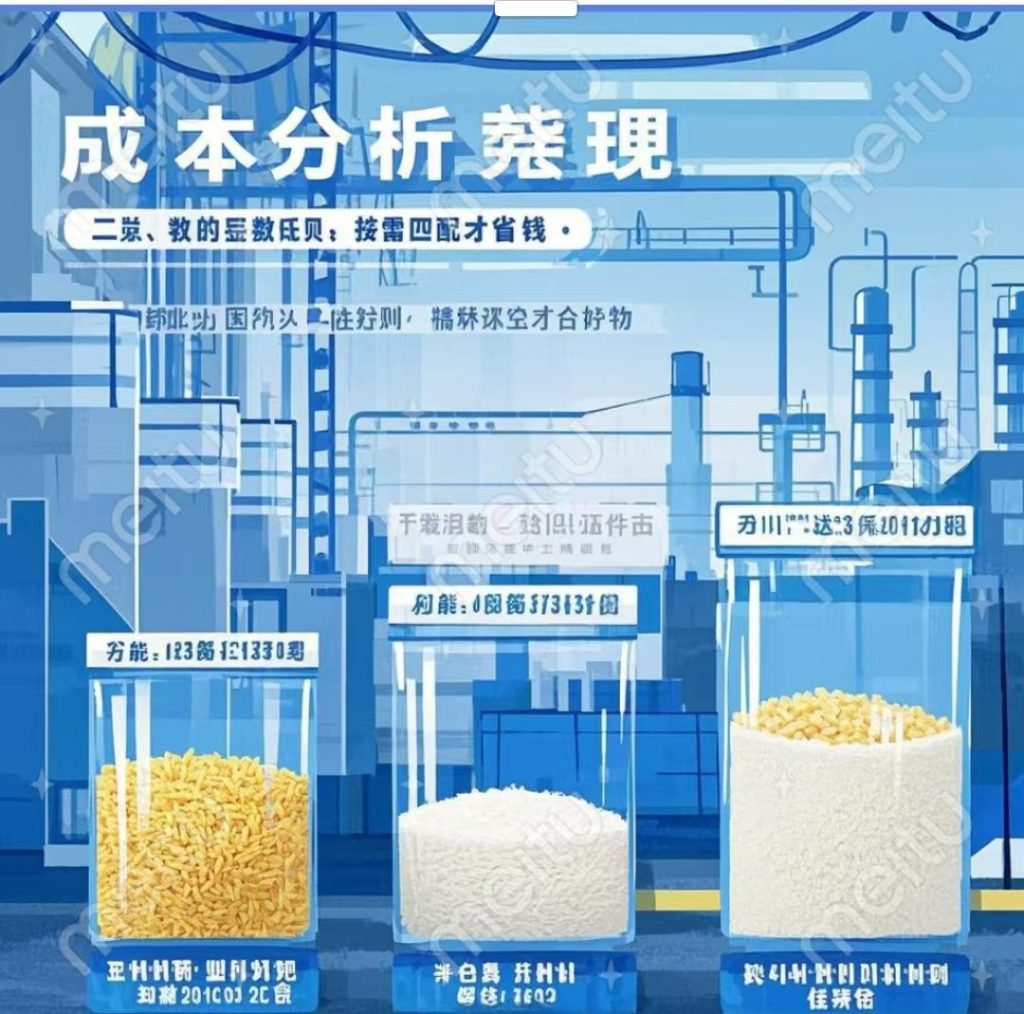
Recommended choice: three-layer film
Reason: Economic comparison (calculated based on 1 ton of goods)
Material cost: The production cost of five-layer film increases by 35%
Logistics cost: The loading volume per container is reduced by 15%
Energy consumption cost: The energy consumption of the film blowing process increases by 28%
Comprehensive cost: The overall cost premium of the five-layer film is 42%
My company uses the co-extrusion technology of Reifenhäuser in Germany to produce modern three-layer films. Through molecular-level optimization, it has achieved 97% of the performance of the five-layer film, with significant cost savings.
Case test:
After a European fertilizer company switched to the three-layer film of Hunan Changjin Petrochemical Co., Ltd., it saved $87,000 in logistics costs annually, and the breakage rate was only 0.09% (the original five-layer film was 0.3%).
Scenario 2: Special demand packaging (professional evaluation required)
Applicable products: hazardous chemicals (anti-static/flame retardant layer required), precision electronic components (super high puncture resistance required), overweight packaging of more than 50kg, extreme transportation environment (below -30℃/sea transportation for more than 60 days)
Recommended choice: five-layer film

3. Breaking the three major cognitive misunderstandings
Misunderstanding 1: “The more layers, the better the quality”
Fact: The puncture strength of the five-layer film is only 3%-5% higher than that of the high-quality three-layer film, but the cost increases by 35%. At the same time, blindly choosing a five-layer film may lead to a decrease in heat sealing (difference in thermal expansion coefficient between layers).
Misunderstanding 2: “Thick film is safer”
Fact: The tensile strength of a 0.13mm three-layer film can reach 42Mpa. Reducing the thickness of packaging film by 10% will save raw material costs of $50,000/1,000 tons of production capacity annually.
Misunderstanding 3: “All suppliers have the same technology”
The truth: The problem of inferior three-layer film often stems from the use of recycled materials, which leads to substandard interlayer bonding process, easy delamination, and reduced film strength.
Our company’s product quality is triple guaranteed:
Raw materials 100% Dow/ExxonMobil virgin PE
Online infrared detection (100% film surface defect screening)
SGS test report for each batch
Contact us:
Changsha Leader Business Consulting Co., Ltd.
📞 Technical consultant hotline: +8615974242566
🌐 Official website: www.leaderbusiness.cn
📧 EMAIL: martin@leaderbusiness.cn